top of page

ADVANCED SPRAY PYROLYSIS MACHINE
MODEL: SPRAYPYINERTATM203




Molten Tin Bath Substrate Heater
AZO Coated glass
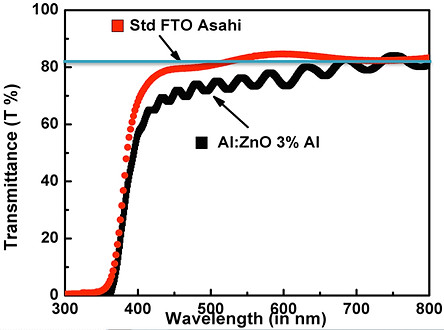
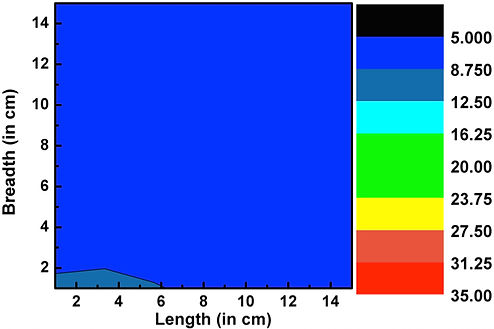
Transmittance Spectra of AZO
Sheet Resistance mapping of AZO coated on glass
ULTRASONIC SPRAY COATING MACHINE WITH ATM. PRESSURE PLASMA NOZZLE
MODEL: ULTRASPRAYPYATMPLASMA304
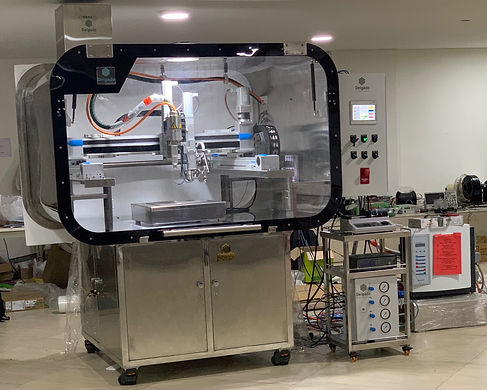
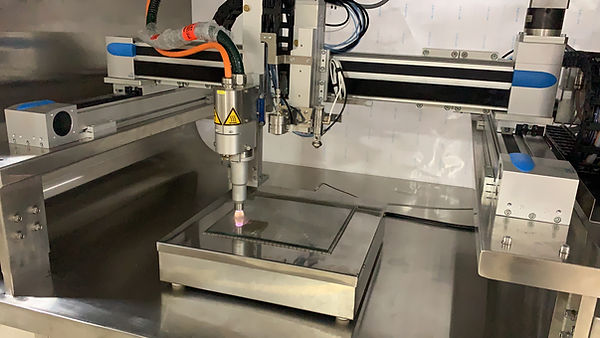
Atm. Pressure Plasma Nozzle in action
ULTRASONIC SPRAY COATER
MODEL: ULTRASPRAYPYATM3451
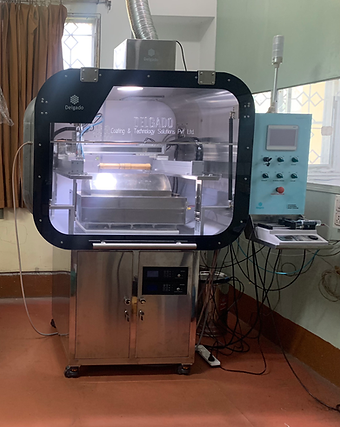

Inside View

Large area TCO coated using Ultrasonic Spray coater
FRUIT COATER
MODEL: SPRAYPYATM301

FRUIT COATER WITH FRUIT REVOLVING ARRANGEMENT
Advanced industry grade PLC controlled electronics
Servo motor controlled precision actuation
Lubricant-free translational stage (Igus, Germany)
100% Food grade Stainless steel body & roller
Anti-Drip Spray nozzle
ELECTROSPINNING MACHINE
MODEL: SPIDERWEB-X-400

Advanced industry grade PLC controlled electronics
Servo motor controlled precision actuation
Customized length of rotational collector (400 mm standard)
Fully Teflon sealed Cabinet inner & 304 grade SS outer chamber
UV-Exposure system of customized wavelength
PID controlled heater inside chamber to control Temperature
De-humidifier inside chamber to control humidity


Five needle Spinneret
Two needle Spinneret

Plate collector
Co-axial Spinneret
Role-to-Role Meta-Material Coating Machine


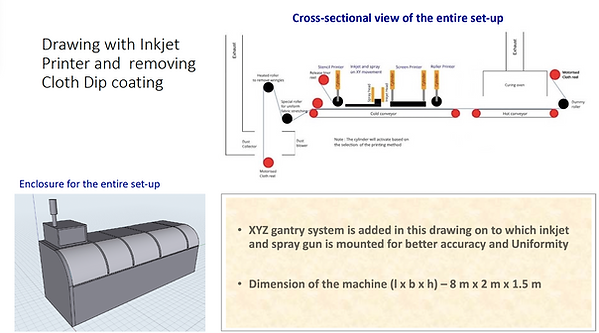
Automatic & PLC controlled
Chemical Vapour Deposition (CVD) System
MODEL: Auto_CVD_1200
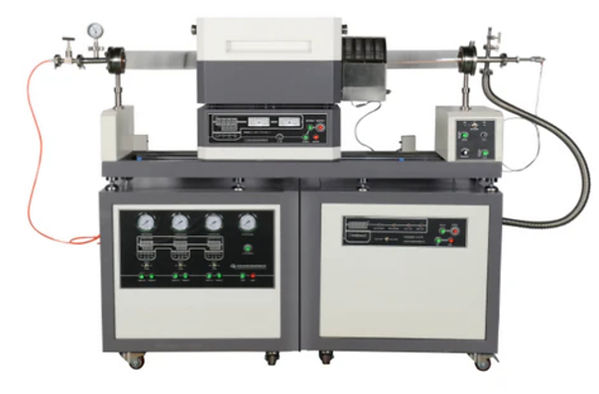
We use Industrial PLC technology for automation and CVD system. By employing an automatic MKS Throttle Valveand a MKS pressure controller which works in conjunction with a Pressure Baratron (pressure transmitter), and a Vacuum pump maintains the required low pressure or vacuum required for the CVD growth process of the material (Graphene in this particular case). With the integration of MKS Throttle Valve and a MKS pressure controller one could ensure stable pressure inside the reactor chamber and repeatability. A PALL filter employed with an activated charcoal chemical Scrubber removes all the harmful chemicals which is the biproduct of growth process.

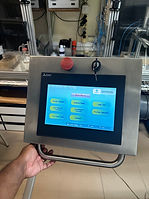
Furnacesystem : 3 Zone
HMI Touch-Screen system
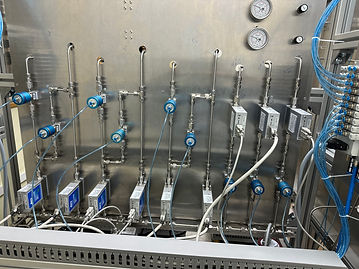

Gals lines with heater
Gas lines with MFCs

PALL chemical FIlter system
bottom of page